Why Rotor Testing?

Detection of rotor bar defects in disassembled motors is a common repair and testing procedure that should be done while a motor is undergoing the repair process. Catching rotor bar defects EARLY in the repair process is key to preventing costly rework, preventing any delays in repair turnaround time, and preventing premature failure of the motor once its back into operation.
If a motor completes the repair process WITH A FLAWED ROTOR, it’s only a matter of time that the motor begins to experience:
- Overheating
- Vibration issues
- Bearing failures
- Mechanical failures
- Efficiency losses
Need a Rotor Tested? Use our Test Stand!
Rotor Testing Services Available. Contact us to learn more!
Rotor Magnetic Field Analysis, a Better Way of Rotor Testing
There are many ways rotors can be tested for defects including dye penetration, ultrasonic testing, growler hacksaw tests, growler iron fillings tests, growler voltage monitoring tests, growler magnetic field viewing film tests, rotor rated flux testing, digital low-resistance ohm-meter measurements (DLRO), and ELCID.
However, many of these testing techniques pose an arc-flash or electrical shock hazard to the operator and they run the risk of damage to the rotor by generating temperatures at the defect locations capable of causing a mechanical deformation of the rotor shaft.
RMFA and sRMFA is different, it does not pose any safety threats and causes no harm to the rotor.
RMFA / sRMFA | Ultrasonic | DLRO | Growler (magnetic film) | Dye Penetration | Visual Inspection | |
---|---|---|---|---|---|---|
Disassembled | X | X | X | X | X | X |
Major Defect Detection | X | X | X | X | X | X |
Electrical Safety | X | X | X | X | X | |
Minor Defect Detection | X | X | X | |||
Repeatable | X | X | X | X | ||
Reportable | X | X | X | |||
Effective on All Rotors | X | X | X | |||
Fingerprinting | X | |||||
Automatic Analysis | X |
Common Test Methodology Deficiencies
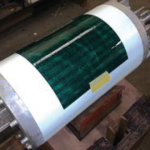
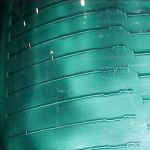
Growler in use with magnetic field viewing film
Many methods of detecting rotor bar defects in disassembled motors lack the sensitivity to find both major and minor defects in cast and fabricated rotors, some even require physically altering the rotor to accommodate testing, such as drilling and taping provisions for test source probe connections. RMFA and sRMFA can locate the major AND minor defects without physically altering the rotor.
- Lacks sensitivity to detect minor flaws
- Physical alteration of the rotor is required for some test methods
- Some methods require a functional stator
- Lacks recordability
- No report generation
- Exposure to arc-flash conditions
How RMFA Works
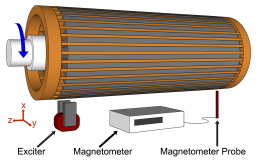
Developed by Brandon and Clark, the RMFA technique consists of an exciter and magnetic field measurement device. The exciter, similar to a conventional growler, along with a variable AC power source, is used to induce current in the cage winding, or bars, of an induction rotor. The magnetic field measurement device, based on a directionally sensitive Hall-effect sensor technology, is used to measure the magnetic field associated with the rotor circuit. Both the exciter and detector are separated from the rotor by a small air-gap to allow the rotor to be rotated during testing. The exciter and magnetic field measurement device, magnetometer, are separated axially along the rotor surface while aligned at the same angle.
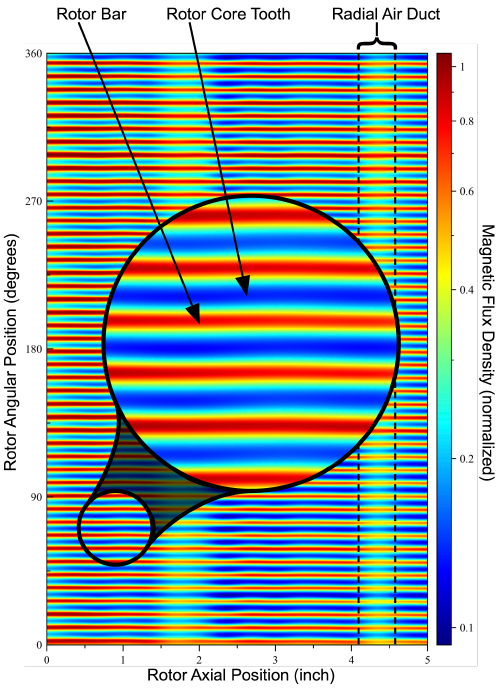
RMFA allows for the localization of damaged or broken rotor cage elements providing an angular position and rotor bar number for any suspected locations of damage. The magnetic flux density pattern produced by RMFA testing are repeatable and encode unique features of a rotors electromagnetic circuit. This RMFA signature is unique to each rotor and can be used to track the aging process of a rotor over time during preventative maintenance shop servicing. Combined with damage detection and the monitoring of RMFA signatures RMFA testing can be used to identify both developed and incipient failures. RMFA provides this advanced defect detection along with numerical testing results appropriate for automatic test interpretation, report generation and trending.
sRMFA (Surface Rotor Magnetic Field Analysis) – is RMFA that has been enhanced to map the entire rotor surface magnetic flux density.
Case Study
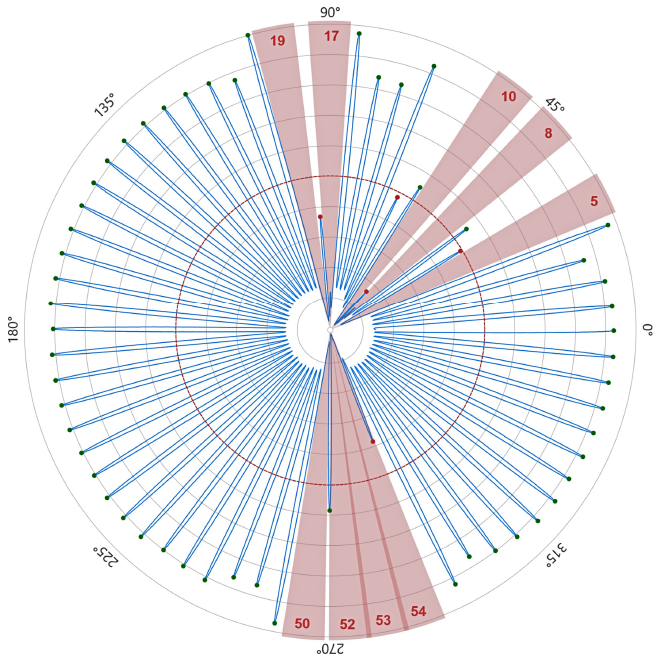
RMFA Case Study:
- Rotor Details: SCI
- Type: Copper, Fabricated, Open-Slot
- Horsepower: 1,500hp
- Speed: 720rpm (synchronous)
RMFA Testing: (Pre-repair)
- Damaged Bars: Qty 5
- Broken Bars: Qty 9
- Total Bars Identified: 68
Want to Purchase a Rotor Test Stand?
Take your motor repair to the next level with RMFA and sRMFA technology.