Gin Control Solutions
Helping you find ways to improving efficiency and meeting the increased quality demands from growers, spinners and consumers. The key is gin controls.
Automating Your Gin
Module Feeder Controls
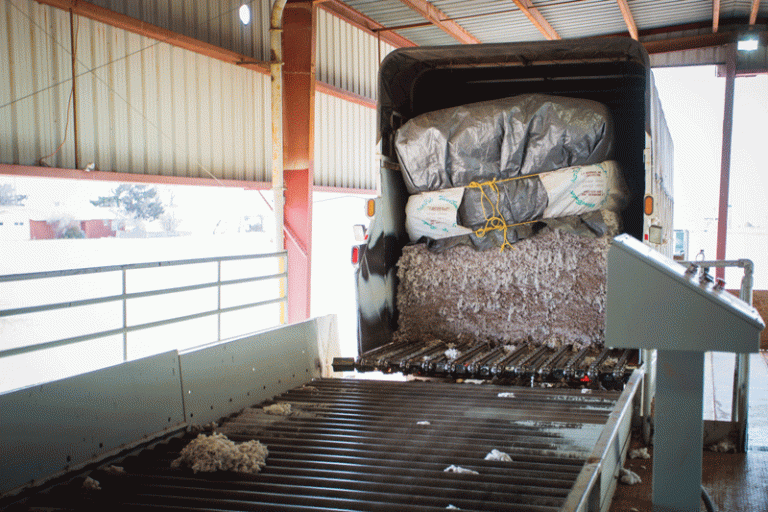
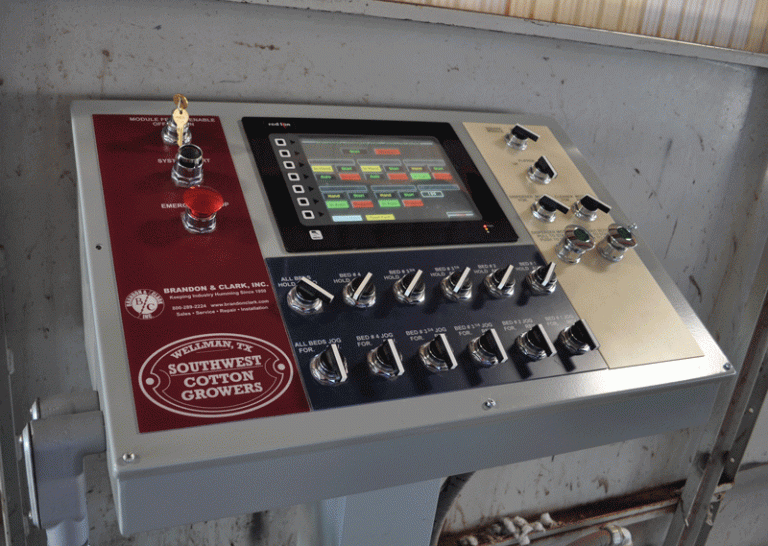
The first entry of cotton into the gin is at the module feeder. The pace at which the rest of the ginning process runs, is at times, dictated at this point. A smooth and steady flow of modules feeding the gin is ideal. It’s the “Goldilocks principle,” not too fast and not too slow, control at the module feeder allows for synchronization of the whole system.
Brandon and Clark’s module feeder controls allows the ginner to be in control at all times. With control over up to five beds at a time, efficiency can be realized.
Operations:
- Controls up to 5 beds
- Controls the disperser operations: forward and reverse
- Feed speed is determined by the ginner
- Easily integrates with existing gin equipment
- Retrofit existing module feeder controls
- Remote unload bed operations
- Hand to auto operations
- Easy to operate
- Monitor bed speed to improve ginning efficiency
Stay in Control at All Times:
- Web browsing capabilities
- 2 Control panels: 1 local and 1 remote display
- Built-in redundancy features ensures that you have control at all times
- Online troubleshooting capabilities
- Monitor switch status remotely
Safety Features:
- Local and remote emergency stops
- Audible and visual alarm system
Gin Stand Controls
The gin stand, the heart of the ginning process. The capacity and potential quality of the produced cotton rests on the proper operation of the gin stand.
An attentive ginner at the gin stand will ensure that the saw cylinder is free to rotate properly and that no foreign objects are within. Once verified, the ginner may distance himself to the integrated gin stand controller, and full operation may commence.
If a need arises and the ginner must come close to the gin stand, Brandon and Clark’s remote swing arm can fully operate the gin stand while still being positioned at a safe distance.
Fire detection is a feature of the Brandon and Clark Gin Stand Controls. If for some reason, too much cotton has entered the gin stand, choking may occur. Choking then causes heating within the equipment, which can quickly become a potential for fire. Because of the seriousness of the matter, fire detection is at the forefront on the gin stand panel as well as at the ginners console.
Leveling and loading conditions are also of great importance. Any unbalance of either is a system running inefficiently. Our controls solution will detect any these undesired conditions alerting the ginner to make adjustments.
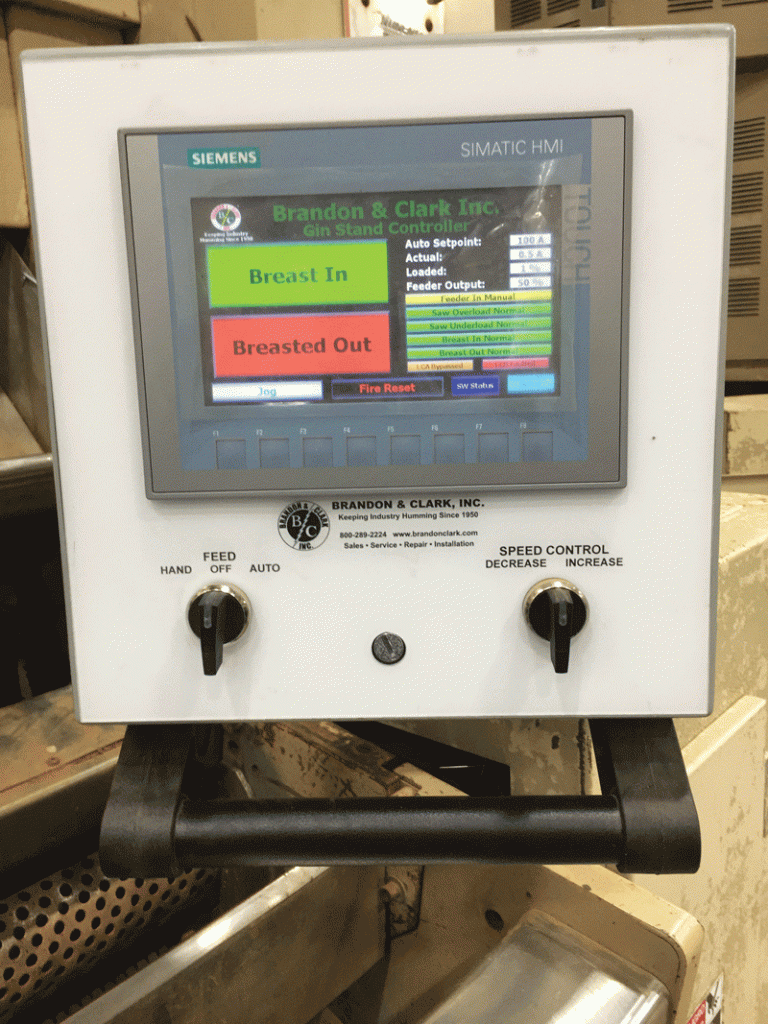
Features:
- NEMA 4 enclosure
- Optional swing arm display
- Touchscreen
- Works with any gin stand
- Fully integrated into ginner console
Touchscreen Operator Display:
- Breasted in/out
- Feed enable
- Set point amperage
- Actual amperage
- Loaded
- Feeder output
- Fire detection
- Low hopper level
- Low discharge flow
- Saw overloaded detection
- Saw unload detection
- Breast in alarm
- Fire reset
Ginner's Console
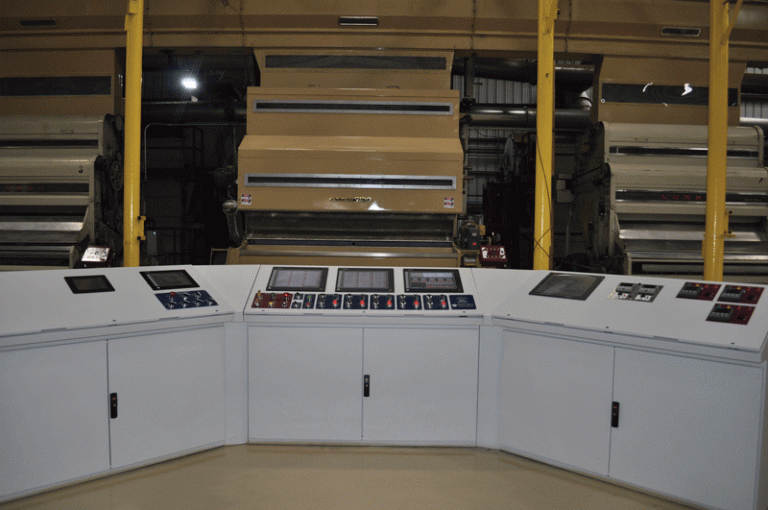
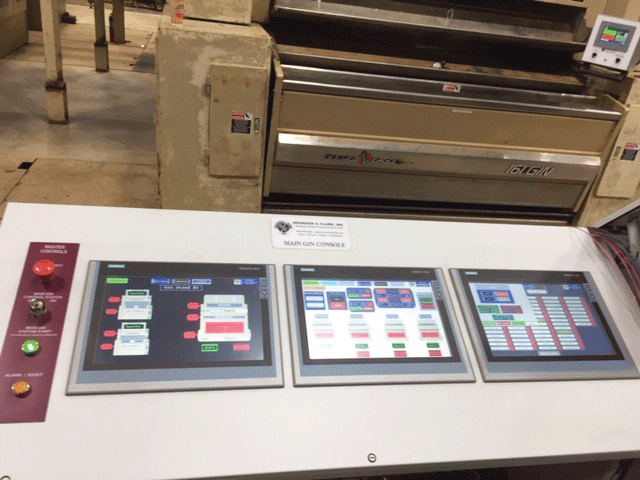
Faster doesn’t always mean better. However fine tuned, clean, constant, and moisture control does equal better. Too much and too fast of a cotton load running through the gin stand drastically effects the finished product. Overloaded gin stands can result in a reduced quality with shorter fiber content and potential seed damage.
Therein comes the Brandon and Clark Ginners Console as a solution for orchestrating the perfect blend of speed and moisture.
At the ginner’s console, moisture levels are being monitored before acceptance of cotton into the gin stand. Based upon each stands load, ramping up or slowing down can be determined. If more time is required in the drying stage, it’s important not to circumvent that process doing so only causes problems down the line.
Features:
- Ginner’s Console gives command beginning at the Motor Control Centers (MCCs) to all the controls overhead
- Signals to the Module Feeder
- Signals to the Press Console
- Gives command to the gin stand when to breast in or turn on main saw motor
- Signals to the Drying System
- Customizable
- Push button, touchscreen or a combination of both for customized operation
Bale Press
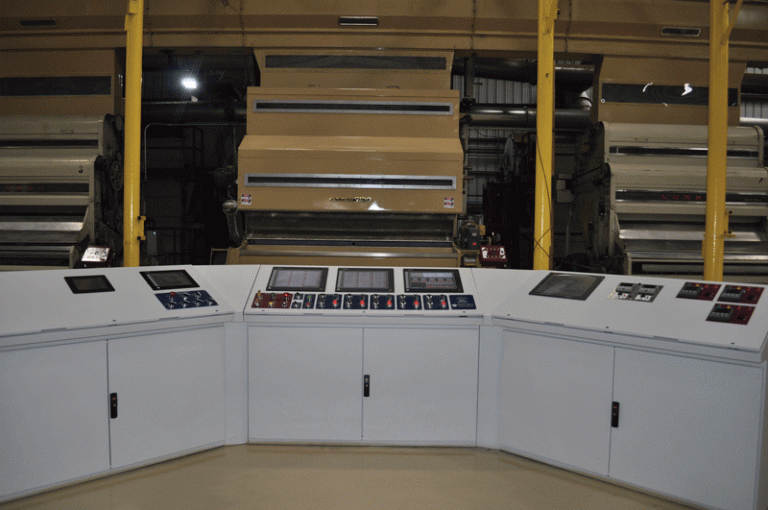
Under the watchful care of the ginner and the unified controls of Brandon and Clark, we have arrived to this final stage of ginning, bale pressing, and it all happened in approximately 3 minutes!
This final stage of cotton processing is bale packaging. This stage consists of the battery condenser, lint slide, lint feeder, tramper, bale press and bale tying.
Bale Press Console Controls:
- Speed
- Hydraulic control
- Bale weight
- Implements compression procedure by controlling the turn speed of the boxes
Lint Cleaner Controls
Uniform and well dispersed cotton leaving the gin stand is key for this next stage, lint cleaning. During the lint cleaning stage, cotton is formed into a batt, this batt is then fed into the saw-type lint cleaner, further removing immature seeds or trash. Controlling a steady pace is important to allow for efficient cleaning and to maintain good fiber.
The lint cleaner has a direct impact on the grade and color of the finished cotton by removing any foreign matter. All ginners have in mind of producing the best quality cotton, but there needs to be mindful decisions about not allowing the cotton to remain in the lint cleaner too long, as this will damage the fiber length. Brandon and Clark’s lint cleaning controls helps the ginner to determine what the ideal length of time should be.
Lint Cleaner Controls:
- Controls condenser screen
- Speed of the lint cleaner screen
- Enables for a better, cleaner process with removal of fine leaves, sticks and other trash material
Battery Condenser Control
The speed in which the battery condenser is operated is again finding the “Goldilocks” sweet spot. Not too slow and not too fast. Matching speed to capacity is key for a smooth and solid batt to be formed. If the speed is too fast, breaks will occur, if too slow the batt will become too thick and can potentially choke the machine.
If the ginner sees an uneven formation of lint batt, also known as “big-ended bales”, he knows that more lint is being deposited at one point of the press box than at the other. Brandon and Clark’s controls will help to prevent this condition by controlling the release of a steady and consistent deposit of batt into the condenser as well as airflow regulation.
Box Turner Retrofitting
Box Turner Retrofitting Can Increase Bales Produced
Brandon and Clark can retrofit your existing box turner and increase its turn rate to significantly turn out more bales per hour!
The average box turn time is 10-12 seconds, we can speed that up to, approximately only 4 seconds!! This improvement to turns can equate to a 2 or more bales produced outcome.
Retrofitting is:
- Quick and easy!
- Requires only a slight modification to the bottom seal and bottom sprocket of your box turner
- Compatible for all press types – above and below ground
- Retrofitting can be accomplished with your current ginning staff
- Any recommended electrical components will be installed by our electrical staff and is backed by our warranty and your 100% satisfaction